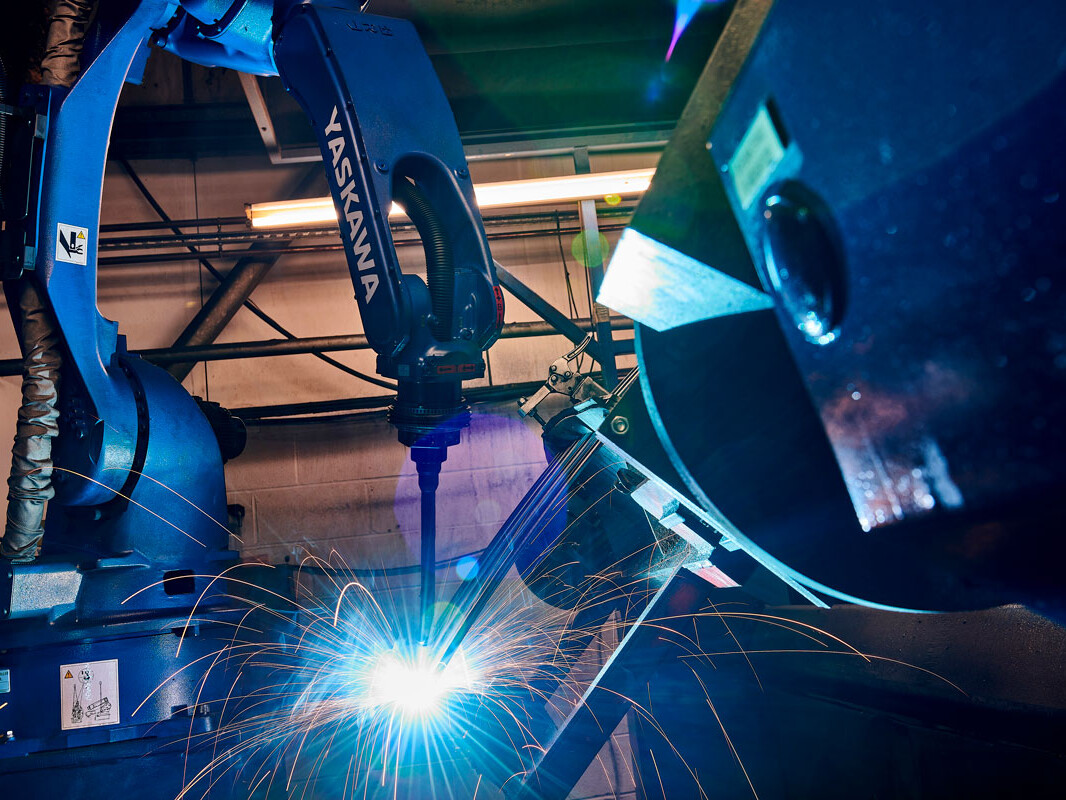
Speed, Reliability and Precision
Robotic welding is a pioneering process that offers increased efficiency through faster and more consistent cycle times. Our six-axis high-performance robots bring speed, reliability and precision to much of our welding work.
We typically use robotic welding for large production volumes and parts required on regular schedules. The process is ideally suited to these applications as the higher cost is mitigated by the volume of output. If quality is paramount, however, then there are significant benefits to using robotic welding for low and medium volume production runs, as well as single items.
We have developed a significant robot welding capacity, with seven robots onsite, two of which were replaced in 2019 in a £150,000 investment.
Our robots can handle metal fabrications up to 5 tonnes and workpieces 8m long and 2.4m in diameter. All of our robots feature two workstations, allowing one piece to be set up while another is being welded, improving efficiency for large assemblies.
More Information
1. Increase in Productivity
Robot welding is often a fast process because it can operate continuously, withstanding a greater arc on-time and moving quickly between weld joint positions. A robotic welding system can provide substantial increases in output.
2. Consistent and Repeatability
Manual welding requires a high level of skill and concentration to achieve reliable consistency. A robotic welder can continue to perform precisely the same weld cycle continuously, 24 hours a day, seven days a week. This is particularly important for complex welds with restricted access, where a robot is able to maintain much greater control.
3. Flexibility
Our robots can be programmed with a vast number of parts, enabling us to simply swap the jig on the robot bed, load the materials and begin the programme.
4. Safety
Robotic welding can improve safety through the reduction of handling and operating within an enclosed cell.
5. Quality
A robotic welder can achieve superior quality by ensuring the correct welding angle, speed, and distance, with repeatable accuracy of ±0.04mm. Ensuring that every welding joint is consistently produced to a very high standard significantly reduces the risk of costly rework.
6. Labour
Robotic welding systems are ideal for alleviating workload during busy periods. These systems allow less experienced welders to consistently perform high-quality welds. Our robot operators are all highly experienced and understand the distinct advantages of using our robotic systems.
7. Reduce Consumables
The consistency of robotic welding allows us to optimise the welding processes, reducing costs associated with welding consumables.
8. Reduced Production Costs
Through improvements in quality, consistency and productivity, a robotic welding system can deliver parts at a reduced cost. Further savings can be made through reduced energy consumption and consumable costs, alongside decreased labour and insurance costs.
9. Reduction in Weld Distortion
Distortion in a weld is due to the expansion and contraction of the weld metal and the adjacent base metal during the heating and cooling cycle of the welding process. A manual process is less repeatable – meaning two qualified welders will have slightly different techniques. If there is a difference in the heat applied, it can create distortions. Robotic welding is both accurate and repeatable, reducing the risk of differences between welds and ensuring consistency.
10. Increased Competitive Advantage
Implementing a robotic welding solution can set companies apart from the competition, allowing for faster completion and delivery of products whilst ensuring consistent quality.