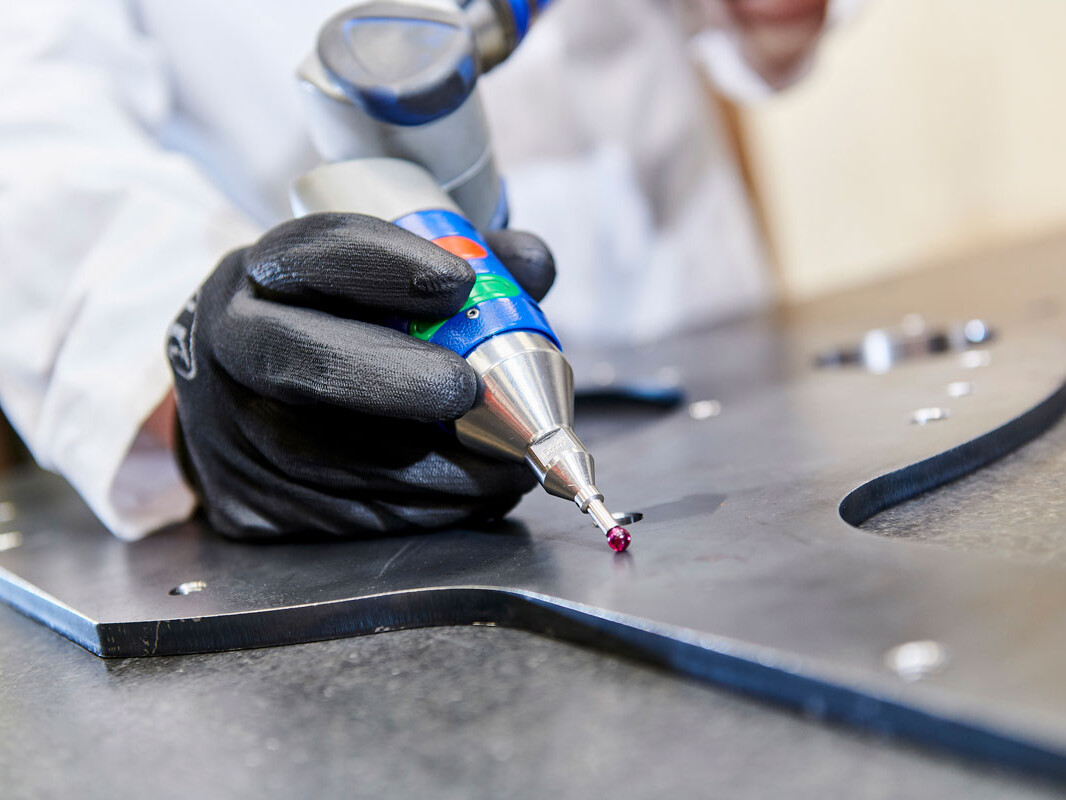
Precision Machining Services
We offer numerous manual and CNC machining services, each backed by our rigorous quality standards and adherence to IATF 16949. Alongside investment in advanced equipment, our precision machinists undertake continuous training to develop a comprehensive skill set. As such, we can work with a wide variety of materials, from common metals like aluminium and steel through to plastics, foams and composites.
Newfield has two primary Computer Numerical Control (CNC) machines, Unisign’s Univers 6000 and Univers 4000. These are used alongside various other machines including a CNC lathe, manual lathe, air tapping drill, pedestal drill and a KRV milling machine.
Univers 6000
The Univers 6000 combines powerful multi-sided precision machining with high dynamics, accuracy and flexibility. It is particularly well suited to large or long workpieces like beams and traverses, axles and trailer side members. It has been used to produce parts for a variety of industries, including oil and gas, commercial vehicle, rail and energy.
The Univers 6000 can maintain accuracy and performance over its entire work envelope, even large workpieces up to 8 metres in length. It can work on toughened materials, accepts large tool diameters and the unique right-angle head allows for multi-sided CNC machining. The large 3 x 0.8 x 0.6 metre working area can also be divided into two zones for pendulum machining, further increasing efficiency.
The Univers 6000’s accuracy is thanks to precise machine geometry and a short distance between the spindle centre line and the Z-axis guide ways – providing high rigidity. The main drive is water-cooled for thermal stability and overall rigidity ensures repeatable operation and manufacture to prescribed tolerances.
Univers 4000
Alongside the 6000, our machinists also use a Univers 4000 vertical CNC machining centre. It is a much more compact system, with a working area of 1.6 x 0.6 x 0.5 metres but is also capable of pendulum machining. It features very high accuracy thanks to precise linear guides on all axes and an automatic tool change from 51 storage pockets.
More Information
Computer numerical control machining, or CNC machining, is the automated removal of material from a block, such as plastic or metal, resulting in a finished part.
A computer converts the design produced by Computer-Aided Design software (CAD), into numbers – or, more correctly, coordinates. The computer uses these coordinates to control the movement of the various tools to remove material and shape the part. The process is also known as subtractive manufacturing and can use a range of complex machinery, from grinders and lathes to mills and routers.
Thanks to its high level of automation, precisoin CNC machining is price-competitive for both one-off custom parts and medium-volume productions. The parts it produces are very accurate with excellent physical properties.
Almost every material can be CNC machined. The most common examples include metals (Aluminium and Steel alloys, brass etc) and plastics (ABS, Delrin, Nylon etc). Foam, composites and wood can also be machined.
The basic CNC process can be broken down into 3 steps.
- The engineer first designs the CAD model of the part
- The machinist then turns the CAD file into a CNC program (G-code) and sets up the machine
- Finally, the CNC system executes all machining operations with little supervision, removing material and creating the part
About the milling process
Milling is the machining process in which rotary cutters are used to remove material by advancing a cutter into a workpiece. This may be done while varying direction on one or several axes, cutter head speed, and pressure. Milling covers a wide variety of different operations and machines, on scales from small individual parts to large, heavy-duty gang milling operations. It is one of the most commonly used processes for machining custom parts to precise tolerances.
Our CNC milling process uses 3-axis milling and 5-axis indexed milling to rapidly cut a choice of more than 30 engineering-grade thermoplastics and metals into complex shapes and precision components.
About the turning process
Turning is a form of machining, a material removal process, which is used to create rotational parts by cutting away unwanted material. The turning process requires a turning machine or lathe, workpiece, fixture, and cutting tool. The workpiece is a piece of pre-shaped material that is secured to the fixture, which itself is attached to the turning machine, and rotated at high speeds. The cutter is typically a single-point cutting tool that is also secured in the machine, although some operations make use of multi-point tools. The cutting tool feeds into the rotating workpiece and cuts away material in the form of small chips to create the desired shape.
Turning is used to produce rotational, typically axis-symmetric, parts that have many features, such as holes, grooves, threads, tapers, various diameter steps, and even contoured surfaces. Parts that are fabricated completely through turning often include components that are used in limited quantities, perhaps for prototypes, such as custom-designed shafts and fasteners. Turning is also commonly used as a secondary process to add or refine features on parts that were manufactured using a different process. Due to the high tolerances and surface finishes that turning can offer, it is ideal for adding precision rotational features to a part whose basic shape has already been formed.
Our CNC turning process uses a rod stock, in a choice of metal materials, which is rotated against live tooling to create final parts with axial and radial holes, flats, grooves and slots.