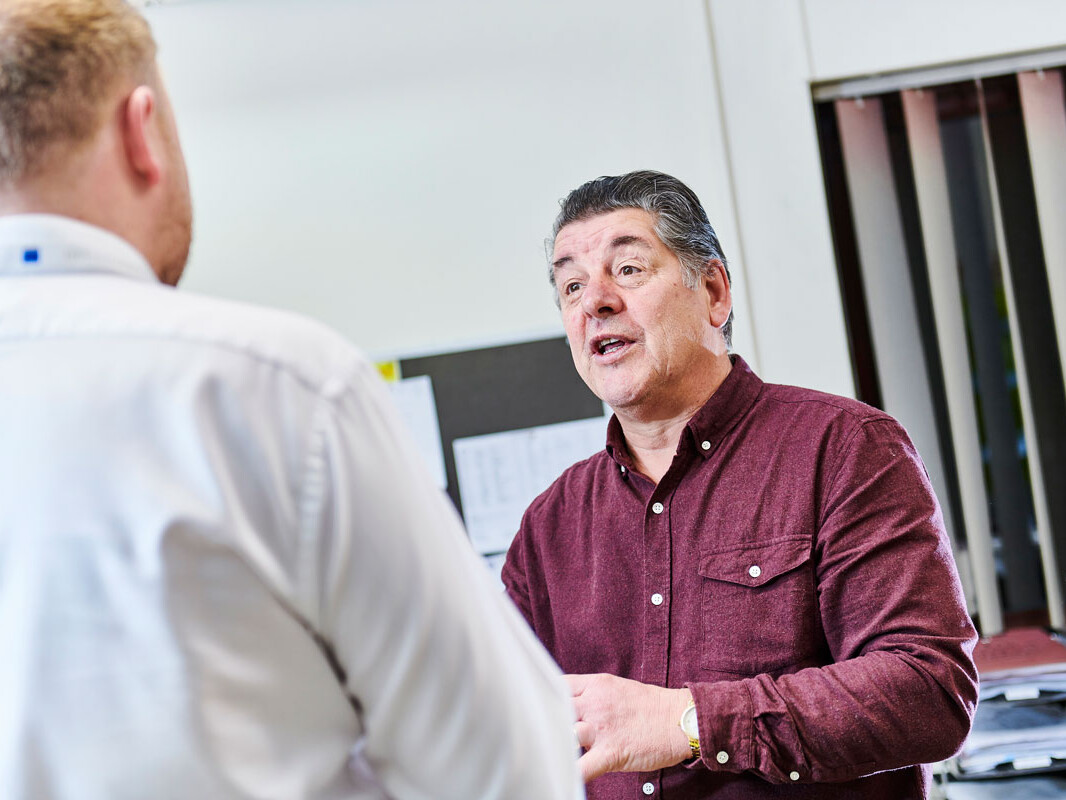
Jig & Fixture Design and Manufacture
Success in the modern marketplace focuses on streamlining production processes. Here at Newfield, our highly skilled Engineering Team do this by utilising the latest technology and software.
Latest Software
Our Engineering team focus on three main areas: New Product Introduction (also referred to as Advanced Product Quality Planning), tooling (jigs and fixtures) and Product Advancement.
Our design engineers consider such things as material thickness, bend radius and batch size to select the most appropriate machines and tooling to produce high-quality components while minimising cost. Many of the metal components manufactured at Newfield undergo punching or laser cutting before metal forming and our engineers will use a job tracker to monitor each part’s progress through the production cycle. The engineering team also uses bending to reduce weld time, forming complex shapes that allow for a reduced component count and minimise welding.
Tooling: Jigs and Fixtures
Jigs and fixtures are required in two instances; when requested by a customer or when the Engineering Team determine that the part is sufficiently complex. For such parts, it is often the case that a jig or fixture is necessary to achieve the required tolerances and ensure dimensional accuracy. Our engineers will always consider how the Poka-Yoke principles can be applied, ensuring that the tooling is as ‘mistake-proof’ as possible.
What is Poka-Yoke?
Poka-Yoke is a Japanese term that translates to “mistake-proofing” or “inadvertent error prevention”. A Poka-Yoke is a mechanism within a process that helps an equipment operator avoid (yokeru) mistakes (poka). Its purpose is to eliminate product defects by preventing, correcting, or drawing attention to human errors as they occur, stopping the operator from proceeding without rectification.
More Information
Autodesk Inventor Info
Autodesk Inventor is a 3D mechanical solid modelling design software developed by Autodesk to create 3D digital prototypes. It is used for 3D mechanical design, design communication, tooling creation and product simulation. This software enables users to produce accurate 3D models to aid in designing, visualizing and simulating products before they are built.
It incorporates integrated motion simulation and assembly stress analysis, whereby users are given options to input driving loads, dynamic components, friction loads and further run the dynamic simulation to test how the product will function in a real-world scenario. These simulation tools enable users designing cars or automotive parts, for example, to optimize the strength and weight of a product, identify high-stress areas, identify and reduce unwanted vibrations, and even size motors to reduce their overall energy consumption.
Autodesk Inventor’s finite element analysis feature allows users to validate the component design through testing part performance under loads. The optimization technology and parametric studies permit users to design parameters within assembly stress areas and compare the design options. Then, the 3D model is updated based on these optimized parameters.
Our Engineering Team also utilises TruTops Boost software for laser nesting as well as programming on our TruBend 230S.
Boost Info
TruTops Boost, the new software solution developed by Trumpf, merges into a single system all the steps needed to generate sheet metal manufacturing programs. This includes everything from part design and data import to nesting and even writing NC programs for cutting, punching and bending. The new operating reasoning makes TruTops Boost easy to understand and, thanks to the Boost Technology, makes it unbeatably fast since the calculations are carried out automatically.
With TruTops Boost, designing and programming for sheet metal processing are made much simpler. The new Trumpf software is based on an entirely new operating philosophy. The program steps the operator through the process and provides support in numerous automatic features. Here, a single system, working on the basis of the job order, handles the design, generates an unfolding, and prepares NC programs for 2D laser cutting, punching and bending. No longer is it necessary to place information in intermediate storage and call it up in various applications.
A jig is a type of tool used to control the location or motion of another tool. A fixture, on the other hand, is a support or work holding device used to fix the object in place. In metal and woodworking, both jigs and fixtures are essential tools. Many often confuse the two but they are two distinct tools with very different functions.
A jig is typically described as a plate, box or open frame used for holding work and guiding machine tools to the work. The main objective of a jig is to provide repeatability, interchangeability and accuracy in the manufacturing process. The most common form of jig is the drill jig, which guides the drill bit to the desired hole location.
A fixture describes the various devices used to hold work in a machine tool. It is a supporting device that is quite large and permanently attached to the work surface. The main objective of a fixture is to ensure that the workpiece is stable and does not move during machining, assembly or welding. A fixture can be unique and built to fit a particular part or shape.
There are also devices that do both the work of a jig and fixture. These are called jigs, which is also why many get confused and find it hard to tell the two apart. There are many types of jigs, some of which includes machining jigs, robot jigs, welders’ jigs, jeweller’s jigs and so on. Some types of jigs are also known as templates or guides.
Just like jigs, there are also various types of fixtures, including general purpose and specialised. Fixtures that are used for general purposes are usually relatively inexpensive and can hold a variety of dimensionally different workpieces. Some examples are vices, chucks and split collets. On the other hand, fixtures can be designed for a special purpose – such as holding specific workpieces for a specific operation on a specific machine or process.
The primary purpose of jigs and fixtures are that they help reduce the cost of production, maintaining consistent quality and maximising efficiency. They enable a variety of parts to be made to correct specifications and reduce operator errors. As they result in increased productivity, easy assembly, reduction in waste and savings in labour cost, jigs and fixtures can substantially reduce the total cost of producing a product.
Poka-Yoke is a Japanese term that translates to “mistake-proofing” or “inadvertent error prevention”. A poka-yoke is a mechanism within a process that helps an equipment operator avoid (yokeru) mistakes (poka). Its purpose is to eliminate product defects by preventing, correcting, or drawing attention to human errors as they occur and preventing the operator from proceeding without rectification.
Correcting defects once they reach the customer is very costly. Every effort must be made to capture defects as early on in the process as possible. It is this early error detection and prevention that makes Poka-Yoke such a powerful tool. The main aim of Poka-Yoke is to ensure that each stage in the chain maintains the expected quality, preventing defects from ever reaching the customer.
Here at Newfield, we utilise the three main methods of Poka-Yoke:
Contact: This method of Poka-Yoke enforces product specification through physical means. For example, if a product has a round shape, the jig holding it would be circular and any other shape would stop the process. Other product qualities such the size, colour and type of material are useful for this kind of mistake-proofing. Sensors on the workbench can detect whether a piece is placed correctly and will stop the process if not.
Constant Value: As the name suggests, this type of Poka-Yoke is triggered when a set quantity is not attained in the process. Here, a process must achieve a predetermined number of steps for it to be considered to be within specifications. Sensors that check if the count meets specifications and reports accordingly.
Sequential: The manufacturing of a product involves a sequence of steps that must be followed in the correct order. This type of mistake-proofing detects whether the preceding step has been done correctly.
In terms of Jigs/Fixtures, this means that we consider any variations that could occur during the assembly process and address these in the design of the tooling to prevent operators making mistakes when assembling the products.
In terms of machinery this means that wherever possible, we add numerical/sequential counters to the machine to verify the number of parts produced.
We also utilise checking fixtures throughout the factory as gauges to ensure the parts conform to their dimensional requirements.