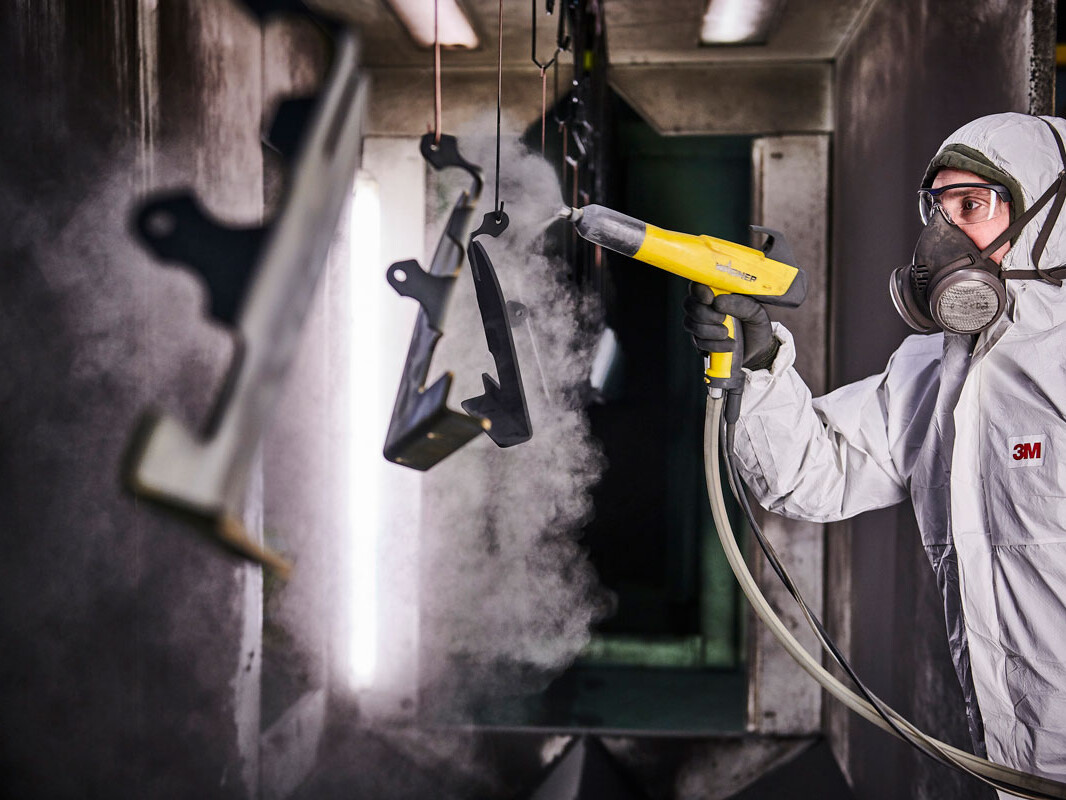
Protection and High-quality Finish
For many of our customers, powder coating is an essential part of their manufacture process, providing both elemental protection and a high-quality aesthetic finish. Newfield offers a diverse selection of powder coating colours at its purpose-built site less than 400 metres from our main facility. We conduct regular quality checks to ensure that all powder coating services are carried out to customer specifications and only use powders supplied by recognised manufacturers. Conforming with the rest of our facility, full traceability and compliance with IATF 16949 and ISO 9001 are maintained throughout the metal powder-coating process. Our metal powder coating meets the ACT (Accelerated Corrosion Test) ASTMD1654 standards and have passed 1008hrs salt spray.
Once the parts have completed and passed their visual inspections, they will either be packaged to customer specifications or transported back to our main site for additional engineering operations, dependent on the specifications of the part.
Benefits of powder coating:
- Powder coating provides a long-lasting, economical, and durable finish with a range of colour options available.
- Powder-coated surfaces are more resistant against scratches, chipping, wear, and fading than other types of finishes.
- It is more environmentally friendly as it does not use solvents and produces few volatile organic compounds.
- As the powder is very fine, it is possible to apply thicker coats without running or clogging. It is typically a one-coat finish.
- The powder coating process includes curing in an oven, creating a protective layer that is much harder than conventional liquid paint.
- Powder coating creates a very even surface finish, vertically and horizontally, because it is sprayed and heated without drips or application traces.
Limitations of powder coating:
- It is harder to achieve a thin finish with metal powder coating.
- The time taken for a colour change is considerably higher for powder coating than wet spray painting, but this includes the time required to perform the quality checks necessary to maintain a high standard of finish.
More Information
What is Powder Coating?
Powder coating is a dry finishing process that has become extremely popular since its introduction in the 1960s, with the global powder coating market expected to reach £9.66bn by 2020. Powder Coating represents over 15% of the total industrial finishing market and is used on a wide array of products.
It is growing popularity thanks to its high-quality, corrosion-resistant finish and aesthetic appearance.
The main difference between a conventional liquid paint and a powder coating is that the powder coating does not require a solvent to keep the binder and filler parts in a liquid suspension.
Intricate fabricated metal shapes can be powder coated evenly and without sagging, allowing for much thicker coats when compared to paint finishes. Powder Coating can be used for both functional and decorative finishes, with an almost limitless number of colours and textures available.
How powder coating works
Powder coatings are based on polymer resin systems, combined with curatives, pigments, levelling agents, flow modifiers, and other additives. These ingredients are melted, cooled, and ground into a uniform powder similar to baking flour. A process called Electrostatic Spray Deposition (ESD) is typically used to achieve the application of the powder coating to a metal substrate. This application method uses a spray gun to apply an electrostatic charge to the powder particles, each of which is then attracted to the grounded part.
After application of the powder coating, the parts enter a curing oven where, with the addition of heat, the coating chemically reacts to produce long molecular chains, resulting in high cross-link density. These molecular chains are very resistant to breakdown and give powder coating its mechanical properties. This type of application is the most common method of applying powders.
Powder coating is based on the principle that objects with opposite electric charges (positive and negative) attract one another. The powder particles are negatively charged after passing through the special spray gun, making them attracted to the earthed part achieving high levels of adhesion and consistency.
Most conducting or thermally stable materials are suitable for powder coating, metals are particularly good due to their high electrical and thermal conductivity. Even complex metal components can be powder coated evenly, with excellent adhesion.
The durability of powder coating
Powder coating is a high-quality finish found on thousands of products you come in contact with each day. It protects the roughest, toughest machinery as well as the household items you depend on daily. It provides a more durable finish than liquid paints can offer, while still providing an attractive finish. It is a tough coating that can resist impact, moisture, chemicals, ultraviolet light, and other extreme weather conditions, reducing the likelihood of scratches, chipping, abrasions, corrosion, fading, and other wear issues.
Pre-treatment process for powder coating
Unlike Iron-Phosphate treatments, Zinc-Phosphate is unable to clean and coat simultaneously and so our 8-stage Zinc-Phosphate process includes cleaning, rinsing and conditioning stages. The reason that we use Zinc-Phosphating over Iron is that Zinc-Phosphate coatings are extremely adherent, they provide a uniform coating with improved coating adhesion properties, better coating in recessed areas and better corrosion resistance and have been widely used in the automotive sector for many years.
Prior to parts undergoing the Powder Coating process, they must first be pre-treated and at Newfield, we operate a Zinc Phosphate pre-treatment process which is comprised of 8 quality-controlled stages:
Stage 1 – Clean
This stage of the pre-treatment process ensures that the parts are free from any residual surface residue such as rust preventative oils and lubricants, machining oils, rolling mill or heat scale, metallic fines and laser scale.
Stage 2 – Rinse
This stage ensures that the part is now free from any excess chemicals from the previous stage and requires the basket to be submerged in constantly agitated clean water for 1 minute.
Stage 3 – Acid
This stage removes any imperfections around the edges of the parts caused by the laser cutting process and ensures any remaining surface contaminants are removed. This process is stringently controlled and monitored through our pre-treatment quality checks which themselves are audited weekly to verify all results.
Stage 4 – Rinse
This stage ensures that the part is now free from any excess chemicals from the previous stage and requires the basket to be submerged in constantly agitated clean water for 1 minute.
Stage 5 – Activate
This stage is used to provide a very uniform micro-crystalline coating which provides maximum effectiveness in the Zinc Phosphate stage.
Stage 6 – Phosphate
This stage involves a chemical reaction between the substrate and the Zinc-Phosphate and is used to provide a uniform crystal layer which the powder then adheres to during the Powder Coating process.
Stage 7 – Rinse
This stage ensures that the part is now free from any excess chemicals from the previous stage and requires the basket to be submerged in constantly agitated clean water for 1 minute.
Stage 8 – Dry
This stage requires the basket to be contained within an oven for 20-30 minutes (dependent on the properties of the part in question) to ensure the part is free from any liquids and that the part is dry and ready to be moved to our paint-line.