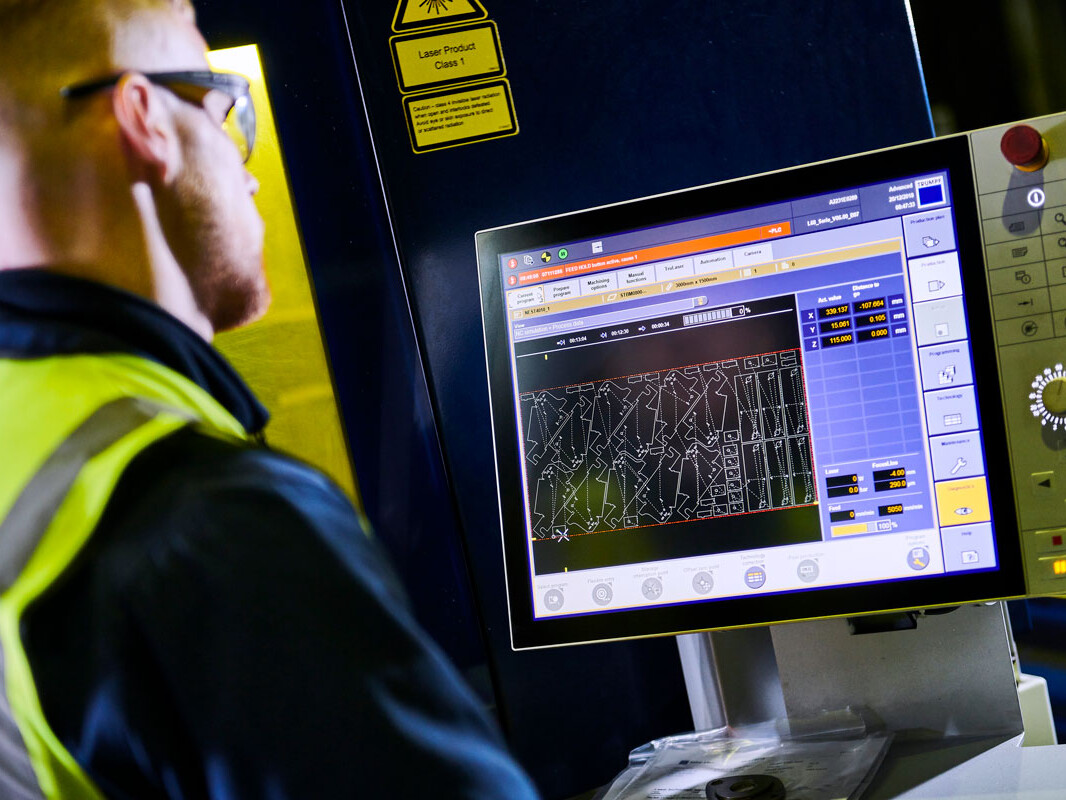
Laser Cutting Service
We continually invest in advanced equipment and staff training to ensure that our processes deliver to customer requirements and IATF 16949 standard. In 2019, Newfield invested over £1.3m in its laser cutting department, greatly enhancing its capacity and capabilities. Our laser operators receive their initial training directly from Trumpf and frequently undertake training to build on their extensive experience, honing their skills and knowledge of laser cutting processes and technologies.
Latest Technology
Our machines offer supreme flexibility, handling profiles from the simplest components to shapes of almost limitless complexity. This versatility extends to both pre-production samples and production batches. CNC laser cutting also leaves clean edges and a high-quality surface finish, requiring less cleaning or additional surface work. At Newfield, we use Nitrogen cutting to eliminate oxidisation at the edges, thereby reducing the required pre-treatment time.
Technical Data
Laser Data
Our Laser Cutting Equipment
We have provided laser cutting services since 1992 and it has quickly become a focal point of our business.
With three Trumpf laser cutting machines, each with a 3 x 1.5-metre sheet metal capacity and automated loading and unloading systems, we have the capacity to meet your needs.
- 5KW 5030 highly specified CO2 and nitrogen machine with semi-automated loading capabilities.
- 8KW 5030 Fibre laser equipped with Liftmaster for semi-automated loading and unloading and the capacity to cut using Oxygen or Nitrogen. We also utilise Trumpf’s Highspeed Eco system upgrade for thicknesses from 4-8mm. In some cases, Highspeed Eco is capable of doubling the machine’s throughput.
- 10KW 5030 Fibre laser which boasts Smart Beam Control (SBC), Active Speed Control (ASC) and a fully automated tower system for loading and unloading.
Find out more about our 10kW Trumpf TruLaser 5030 here
Newfield uses an advanced CADCAM system, Boost, to produce the CNC code which enables components to be programmed quickly and accurately, ensuring there are no delays leading up to, or during, production. It also merges all the steps needed to generate sheet metal manufacturing programs into a single system, including everything from part design and data import to nesting and even writing CNC programs for cutting, punching and bending.
More Information
Laser cutting technology offers supreme flexibility and is capable of creating simple profiles through to highly complex shapes. It uses a high-energy infra-red laser beam and a focusing lens to concentrate energy to a fine point. This causes rapid localised melting and partial vaporisation of the material. Nitrogen gas is directed through a nozzle and blasted at the surface, removing excess molten material and prevent oxidisation. The laser can be used to cut out patterns and shapes from flat sheet metal or piping.
On a precision laser cutter, the head moves over the sheet metal plate in a precise prearranged pattern, maintaining a highly accurate distance between the cutting head and the metal plate. Compared to mechanical cutting, lasers offer better material management, lower energy consumption and more precise and cleaner edges.
Lasers can be used on a variety of materials but are ideally suited to large sheet metal plates made of mild steel, stainless steel and aluminium. It is a very accurate process and causes minimal heat damage to the material. The accuracy, quality and consistency of the cut mean that lasers can be used to cut intricate shapes, elaborate patterns and small holes.
What is Kerf?
The laser burns away a portion of material when it cuts through. This is known as the laser kerf and ranges from 0.08mm – 1mm depending on the material type and as well as other factors. Any areas in your design where cut-lines are closer than 0.5mm together could burn away entirely. Any details narrower than 1mm are likely to be very fragile and in some cases can cause the material to warp whilst cutting. As a benchmark, it is recommended that minimum cut widths be no smaller than the corresponding thickness of the material.
For example, if cutting from 3mm mild steel, it’s best not to allow any widths less than 3mm. We can go smaller, but this can make your pieces very fragile and therefore susceptible to defect during the manufacturing process. Our engineering team will advise if your drawing has cutting tolerances that are too small and will work with you to resolve the issue.
Kerf is determined by material properties and thickness. But other factors also have an impact on how much the laser removes. The focal length of the lens, as well as pressure of the compressed air, can both have an impact. Kerf widths can vary even on the same material sheet, whether cutting a straight line or a curve line or from laser cutting in the X or Y-Axis. The manufacturing tolerance of the material can also impact the kerf.
There are many other parameters that also affect cut quality, but when all are controlled properly, laser cutting is a stable, reliable, and very accurate process.
TruTops Boost
At Newfield, we use TruTops Boost software to help generate sheet metal manufacturing programs. It aides with everything from part design and data import to nesting and writing cutting programs. The software makes sheet metal processing quicker and more intuitive, increasing productivity while ensuring high-quality output.
With TruTops Boost, designing and programming for sheet metal processing are made quicker and more intuitive than ever before. It provides our engineers with the latest version of all current job orders, displaying their status within the current process step. It also immediately recognises when a design specification has been changed, automatically adjusting the upline or downline steps and notifying the operator if there is a need to intervene. The software also considers all available technology when processing part data, ensuring that the best methodology is implemented.
Thanks to Newfield’s recent investment in a new TruBend 230S cell, this software is also being used by our Press Department.
Productive processing, smooth processes
Our TruLaser 5030 fibre is capable of both high processing speed and consistent, high part quality – even for complex contours. It achieves excelled feed rates thanks to its advanced solid-state laser. Newfield’s 5030 uses a suite of assistant systems to accelerate the machining process, increasing productivity and reliability. Operator involvement is minimal with numerous autonomous capabilities, increasing uptime. Listed below are some key features of Newfield’s 10KW TruLaser 5030 fibre.
- High machine dynamics: the 5030 can effortlessly handle complex contours in both thin and thick sheets. It has been designed to operate at maximum capacity and high feed rates without compromising quality.
- Process reliability: even in fully-automated operation, the 5030’s Smart Nozzle Automation ensures that the nozzle and lens are kept in excellent cutting condition. The CoolLine function allows the user to perform delicate cutting operations in thick steel by cooling the workpiece. This also enables new and complex geometries as well as more efficient sheet configuration and reliable processing of thick material.
- Extremely fast: The 5030’s Highspeed Eco mode allows for up to 100% greater productivity while a patented nozzle reduces nitrogen gas consumption by up to 70%. This process is ideal for structural steel and stainless-steel sheets with no reduction in quality.
- Part quality: for the highest possible part quality, the 5030 uses BrightLine fibre – a combination of special optics and flow-optimised nozzles.
- Semi-autonomous operation: Thanks to the 5030’s Active Speed Control, the system can see through the nozzle and into the kerf, monitoring the cutting process and regulating feed rate automatically. Active Speed Control also works with variations in material thickness and surface quality, such as rust or traces of coating. It prevents disruption of the cutting process thereby reducing the number of rejected parts significantly.
Stainless Steel and Non-Ferrous Metal
The Result:
CO2 Laser:
Exceptional part quality with extremely smooth and partly reflective edges – with BrightLine for thick sheet metal, and without BrightLine for thin sheet metal. Virtually no burr formation.
Solid-State Laser:
Excellent part quality with thin sheet metal, assisted by BrightLine fiber with thicker sheet metal to ensure a consistent sectional view.
Structural Steel
The Result:
CO2 Laser:
When carrying out flame cutting (with oxygen), both laser beam sources achieve the same level of quality. When carrying out fusion cutting (with nitrogen), the CO2 laser outperforms the solid-state laser.
Solid-State Laser:
A slight burr forms when carrying out fusion cutting.
TruLaser Series 5000
Maximum Dynamics
The productive machines in the TruLaser Series 5000 can effortlessly handle both thin and thick sheets. With the TruDisk 10001 and highly dynamic drives, they enable highly productive and reliable manufacturing across the entire range of sheet thicknesses. The machines in this range are designed for maximum capacity and are able to convert these high feed rates into sheet throughput.
Producing with Process Reliability
Ensuring that the nozzle and lens are in the best possible condition is an important prerequisite for achieving reliable processes and high part quality. Smart Nozzle Automation combines intelligent functions that ensure just that – even in fully automatic operation. With the CoolLine function, you can perform delicate cutting operations, even in thick structural steel. This function cools the workpiece during cutting and enables new geometries, more efficient sheet configuration, and reliable processing of thick structural steel.
Extremely Fast
The Highspeed Eco cutting process enables you to get even better performance from your laser machine. When carrying out nitrogen cutting, this method enables you to nearly double your feed rate and sheet throughput when processing medium and thick structural steel and stainless steel sheets, without any reduction in quality: Highspeed Eco even prevents burr formation on contours with sharp edges.
Top Part Quality
BrightLine fiber combines special optics with flow-optimized BrightLine nozzles and the switchable 2-in-1 cable. The result of this is that you achieve maximum part quality. The high- quality cut edges ensure that your parts do not get caught during removal, saving you a great deal of time.
Unrivaled Economical
With an efficiency rate of over 30%, the energy consumption of a TruDisk solid-state laser is exceptional. The Highspeed Eco function helps you to achieve cutting gas savings of up to 70% – thanks to a patented nozzle design.